DX推進記#6:保持炉をDXする
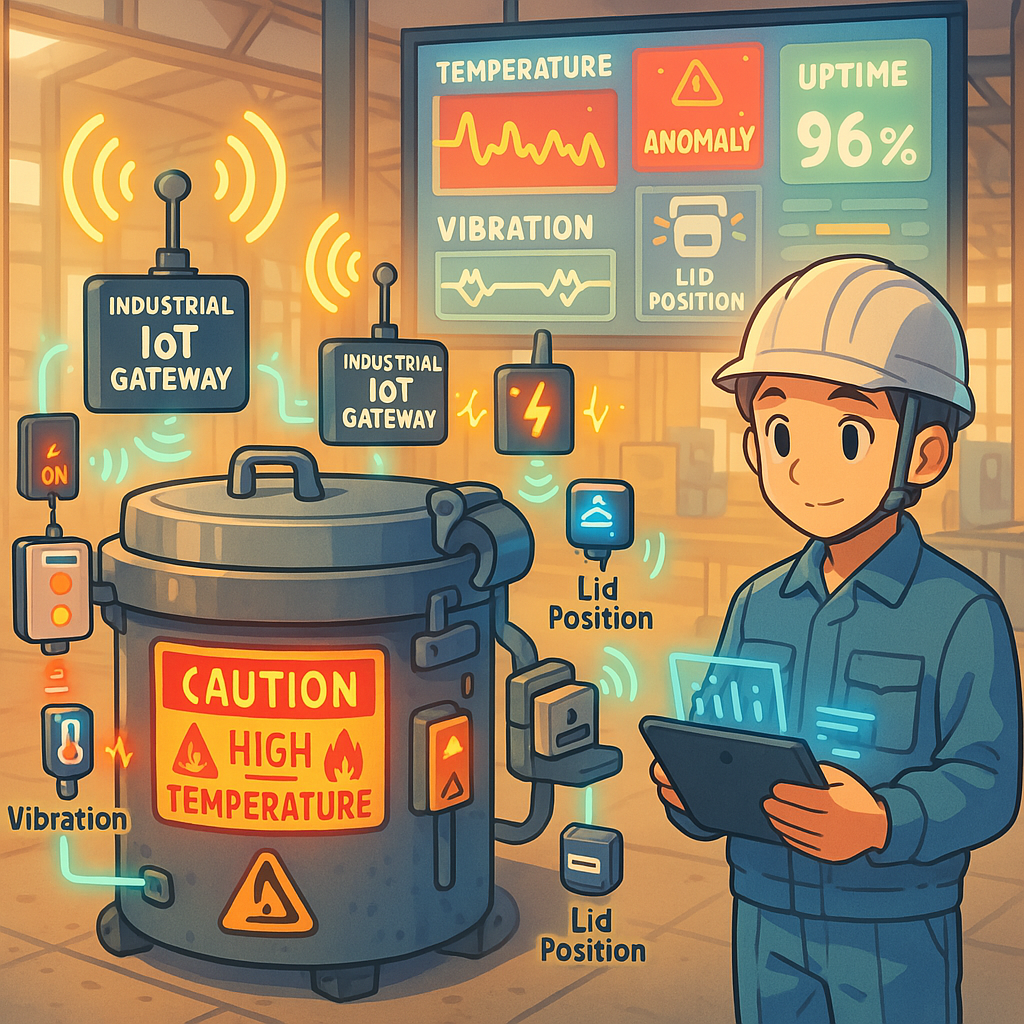
当社ではDXに向けた取り組みを段階的に進めてきて、現在ではある程度その実現に成功しつつあります。数回にわたり当社のDXの推進記を紹介しております。
IoTを活用した保持炉モニタリングの取り組み
製造現場におけるIoT導入には、技術的な工夫だけでなく、現場特有の運用制約に対する理解と対応が不可欠です。今回取り組んだ保持炉のモニタリングプロジェクトは、そうした制約の中で実現されたチャレンジでした。
導入先のお客様には、以下のような現場の課題がありました。
- 一度停止すると、炉内の溶湯が固まり、再稼働までに多くの時間とエネルギーを要する
- 万一湯漏れが発生すると、火災につながるリスクがある
- 保持炉の蓋の開閉を最小限に抑え、無駄な電力消費を削減したい
こうした背景から、炉の状態を常時監視し、異常の兆候を早期に検知できるIoTシステム(炉プラス)の導入をご提案しました。
システム導入にあたっての方針
IoTシステムを導入するにあたり、主な制約や要件は以下のようなものでした。
- 現在の設備を変更せずに、必要なデータを取得できること
- 24時間365日、ノンストップでデータを取得し続けられること
- 異常時にはアラームが即時発報されること
- 収集したデータを活用して、レポート作成や運用改善につなげられること
この方針を実現するために、現場環境に強く、設置後の保守負荷が少ないIoTデバイスを選定し、シンプルかつ安定したシステム構成を追求しました。
実装内容と技術的な工夫
今回のシステムでは、配電盤に電流センサーを設置し、過電流や断線の兆候をリアルタイムで監視できるようにしました。また、IoT機器の電源についても同じ配電盤から取得する構成とし、外部電源に依存することなく、安定した電力供給を確保しました。これにより、長期間にわたって安定したセンシング環境を実現し、炉の運転に影響を与えることなくシステムを稼働させることが可能となりました。
システム設計においては、IoTデバイスを用いたセンシング部と、Web側での処理を明確に分離しました。IoTデバイスは、温度や電流といった基本的なセンサーデータの取得に専念させることで、現場でのトラブルを最小限に抑えながら高い安定性を維持しています。収集したデータはWeb上で蓄積・処理され、異常の検知や通知、さらには長期的な稼働傾向の分析、今後のシステム拡張や機能追加まで、柔軟かつ効率的に対応できる設計としました。
成果
これまでの運用において湯漏れや重大な障害は発生していないものの、本システムによって設備の状態を常時モニタリングできていることで、安定稼働が維持されているという確認と安心感を得られています。万一の異常に備える体制が整ったことで、現場のリスクマネジメントにも寄与しています。
また、ここで取得した稼働データは、先日上市した新型省エネ炉の設計・検証にも活用されました。特に、電力使用状況や加熱制御の変動といった実際の運用条件をベースに、電力制御の安定性に関する実証を行うことができ、開発段階での技術的な裏付けができました。
当社のIOTに興味のある方はこちらをクリックー→ https://roplus.cast-rev.com/
当社の新型省エネ炉に興味のある方はこちらをクリックー> https://lp.cast-rev.com/IRMseries/
アルミ鋳物・ダイカストに関する
課題を解決します
溶融品質
を上げたい製品歩留まり
を改善したい製品長寿命化
を図りたい自動化・省力化
を進めたい省エネ
を追求したい